Stents
MeKo pioneered stent manufacturing as early as 1995. Today, we are among the world's largest contract manufacturers of stents and are perceived as quality leaders. Thanks to unique manufacturing processes and our expertise, we also realize the most demanding projects.
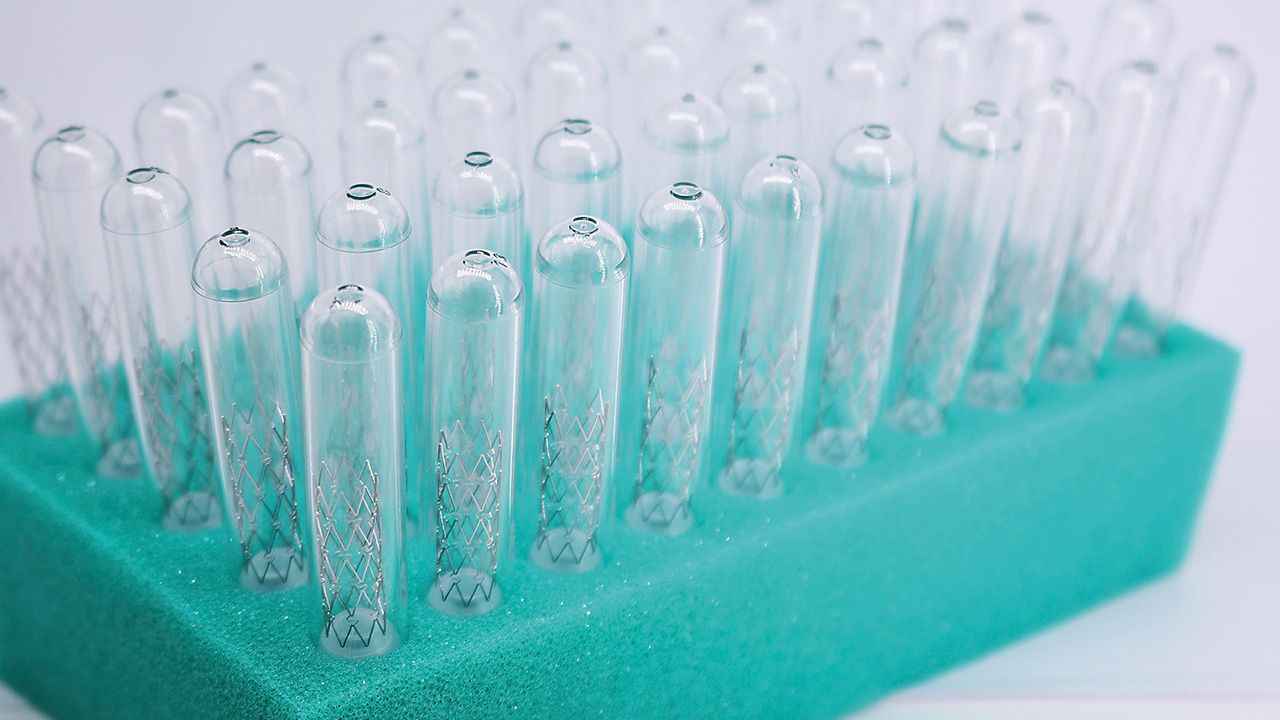
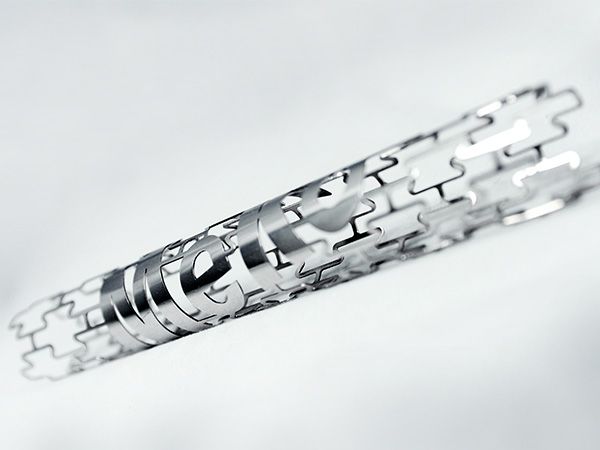
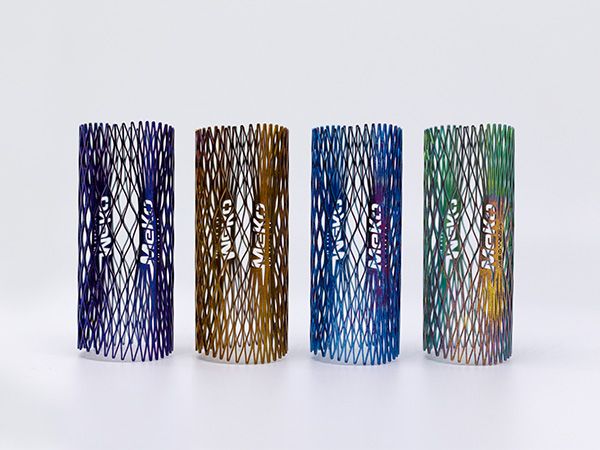
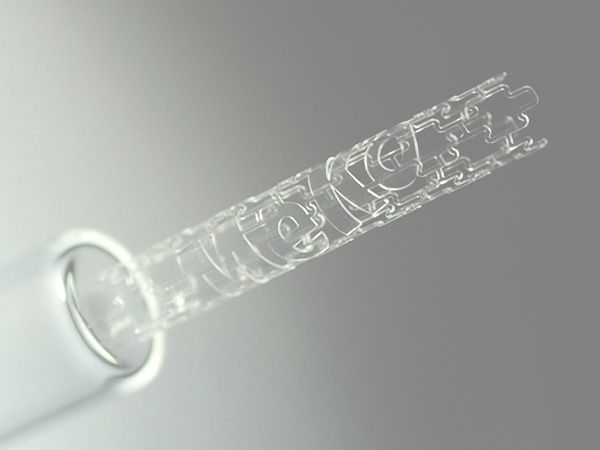
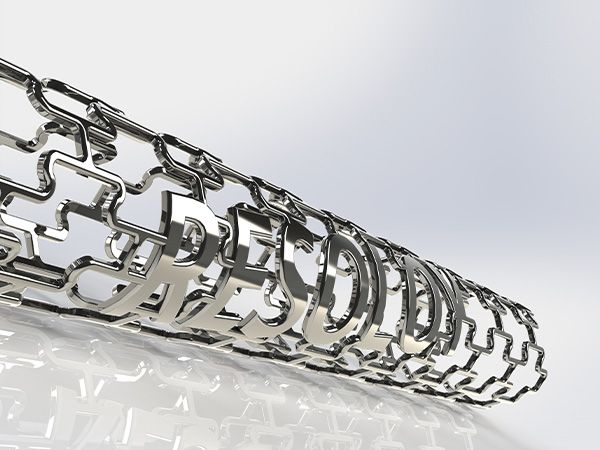
From Tube to Stent
Every stent at MeKo starts as a tube. Various sizes and materials such as Nitinol, 316L (316LVM), L605, MP35N, and Phynox are laser-cut. More than 2,000 certified tube batches are available in our inventory, ensuring rapid prototyping.
Bioresorbable Stents
Bioresorbable stents are made from degradable metals such as magnesium (e.g., MeKo's RESOLOY®), iron, and zinc, as well as polymers (e.g., PLLA). We advise our customers on tube selection but also process customer-supplied material.
Precision Laser Cutting
Our self-developed special laser systems enable highly precise manufacturing with burr-free cut edges. Tolerances of a few µm are not a problem. Experience full flexibility for your stent design, with almost no restrictions in length and diameter. At MeKo, every stent begins as a tube.
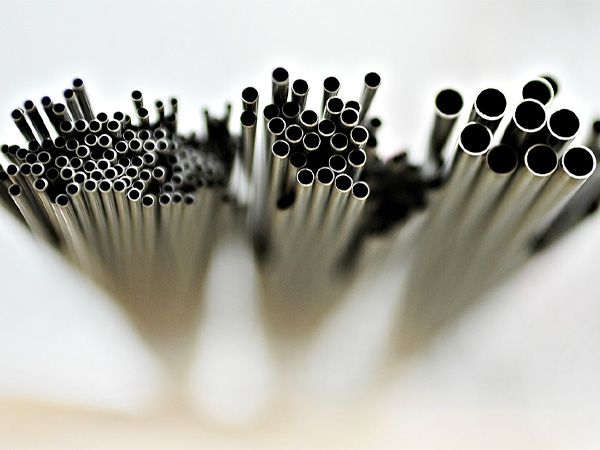
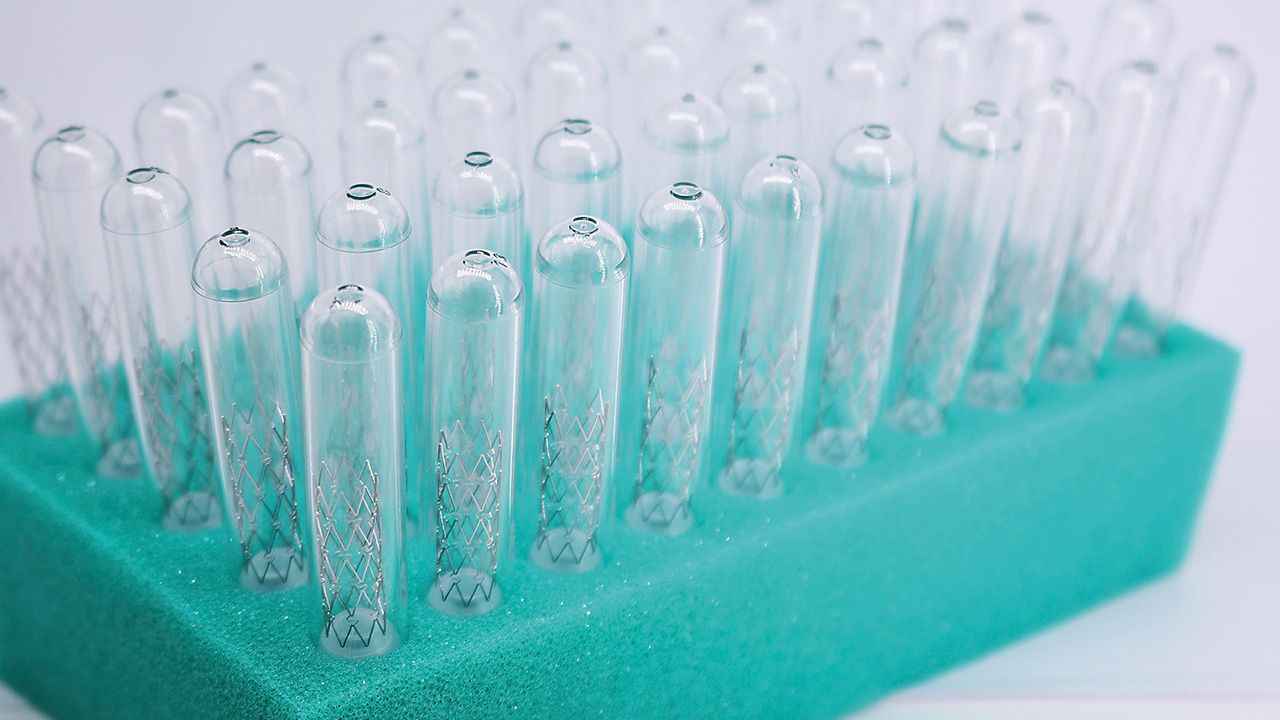
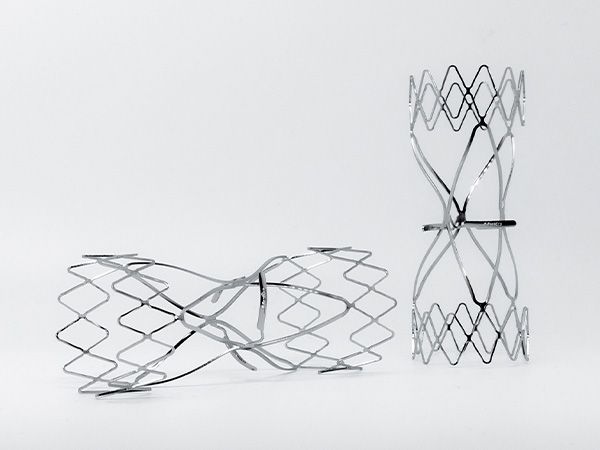
Post-Processing of Stents
Trust MeKo with the manufacture of your next stent design.
Thanks to electropolishing at MeKo, the stents receive an exceptionally smooth stent surface.
MeKo's heat treatment produces the world's smallest grain sizes (ASTM11 for 316L/316LVM) for higher corrosion resistance and smoother surfaces after stent dilation. Our specialty process, LowElast, optimizes the crimping behavior of L605 stents.
A core competency is the shaping and adjustment of the Af temperature in the heat treatment of Nitinol components.
MeKo's passivation process ensures higher biocompatibility. Our specialty process, CoReSurf, guarantees perfect corrosion resistance of stents for better clinical results.
The surface adhesion of drug coatings has been improved through surface modifications like ModiSurf+.